Products
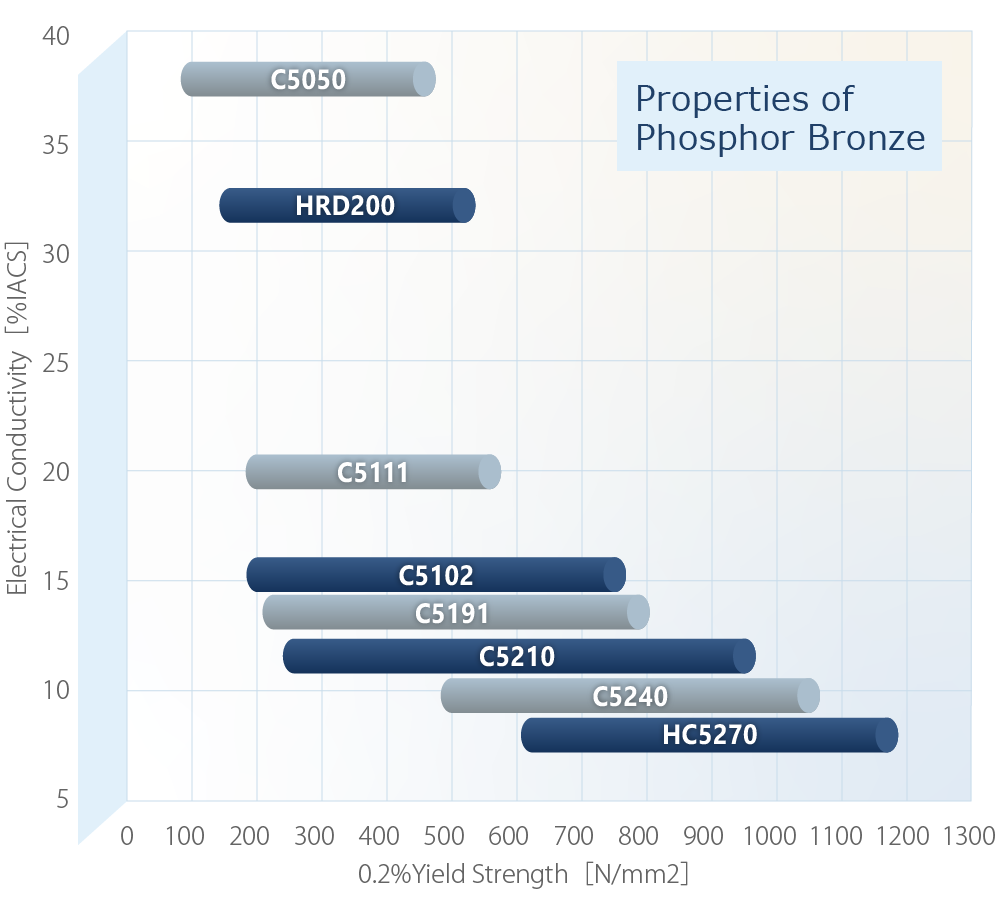
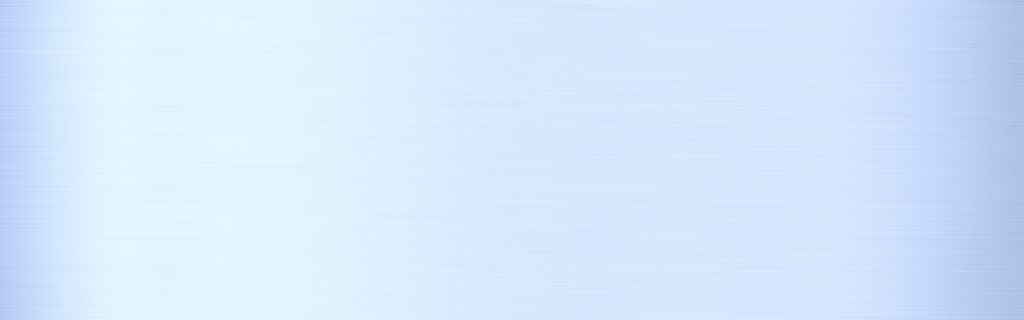
Phosphor Bronze Plates and Strips
*Please contact us if you have any specific requests regarding chemical compositions, mechanical properties, and thicknesses.
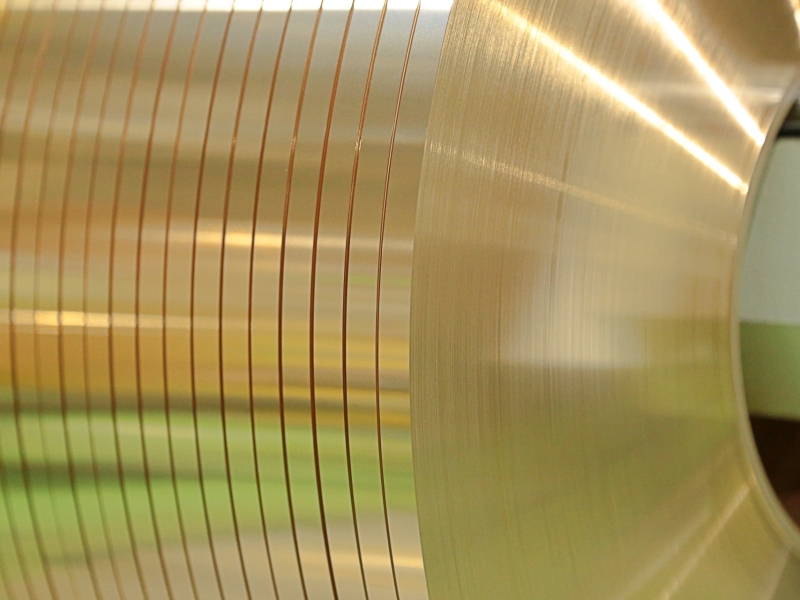
Physical Properties
Alloy Number | (unit) | C5050 | HRD200 | C5111 | C5102 | C5191 | C5212 |
---|---|---|---|---|---|---|---|
Specific Gravity | - | 8.89 | 8.87 | 8.86 | 8.86 | 8.82 | 8.80 |
Coefficient of Thermal Expansion | 10-6 /K | 17.8 | 16.5 | 17.8 | 17.8 | 18.2 | 18.2 |
Thermal Conductivity | W/m・K | 205 | 152 | 84 | 71 | 67 | 63 |
Electrical Conductivity | %IACS | 38 | 32 | 20 | 15 | 14 | 12 |
Specific Heat | J/Kg・K | 377 | 377 | 377 | 377 | 375 | 377 |
Modulus of Elasticity (Tension) | kN/m㎡ | 118 | 122 | 110 | 110 | 115 | 110 |
Chemical Composition
Alloy No. | Chemical Composition(%) | |||||
---|---|---|---|---|---|---|
Sn | P | Fe | Pb | Zn | Cu+Sn+P | |
C5050 | 1.0~1.7 | ≦ 0.15 | ≦ 0.10 | ≦ 0.02 | ≦ 0.20 | ≧ 99.5 | HRD200 | 1.7~2.3 | ≦ 0.15 |
C5111 | 3.5~4.5 | 0.03~0.35 | ||||
C5102 | 4.5~5.5 | |||||
C5191 | 5.5~7.0 | |||||
C5212 | 7.0~9.0 |
Mechanical Properties
Alloy No. | Temper | Tension Test | Hardness Test | |||
---|---|---|---|---|---|---|
Thickness Category ㎜ |
Tensile Strength N/m㎡ |
Elongation % |
Thickness Category ㎜ |
Vickers Hardness HV*1 |
||
C5050 | O | ≧ 0.10 ,≦ 5.0 | ≧ 240 | ≧ 40 | - | - |
1/4H | ≧ 0.10 ,≦ 5.0 | 240~330 | ≧ 30 | ≧ 0.15 ,≦ 5.0 | 60~120 | |
1/2H | ≧ 0.10 ,≦ 5.0 | 330~450 | ≧ 10 | ≧ 0.10 ,≦ 5.0 | 90~155 | |
H | ≧ 0.10 ,≦ 5.0 | 390~500 | ≧ 3 | ≧ 0.10 ,≦ 5.0 | 120~165 | |
EH | ≧ 0.10 ,≦ 5.0 | ≧ 460 | - | ≧ 0.05 ,≦ 5.0 | ≧ 140 | |
HRD200 | O | ≧ 0.10 ,≦ 5.0 | ≧ 300 | ≧ 30 | ≧ 0.10 ,≦ 5.0 | 70~115 |
1/2H | ≧ 0.10 ,≦ 5.0 | 400~500 | ≧ 10 | ≧ 0.10 ,≦ 5.0 | 125~165 | |
H | ≧ 0.10 ,≦ 5.0 | 450~550 | ≧ 5 | ≧ 0.10 ,≦ 5.0 | 150~185 | |
EH | ≧ 0.10 ,≦ 5.0 | 500~600 | ≧ 2 | ≧ 0.10 ,≦ 5.0 | 175~205 | |
SH | ≧ 0.10 ,≦ 5.0 | 600~700 | - | ≧ 0.10 ,≦ 5.0 | 185~215 | |
C5111 | O | ≧ 0.10 ,≦ 5.0 | ≧ 295 | ≧ 38 | - | - |
1/4H | ≧ 0.10 ,≦ 5.0 | 345~440 | ≧ 25 | ≧ 0.15 ,≦ 5.0 | 80~150 | |
1/2H | ≧ 0.10 ,≦ 5.0 | 410~510 | ≧ 12 | ≧ 0.10 ,≦ 5.0 | 120~180 | |
H | ≧ 0.10 ,≦ 5.0 | 490~590 | ≧ 7 | ≧ 0.10 ,≦ 5.0 | 150~200 | |
EH | ≧ 0.10 ,< 0.20 | 570~660 | - | ≧ 0.05 ,≦ 5.0 | 170~220 | |
≧ 0.20 ,≦ 5.0 | ≧ 3 | |||||
SH | ≧ 0.10 ,≦ 5.0 | ≧ 640 | - | ≧ 0.05 ,≦ 5.0 | ≧ 200 | |
C5102 | O | ≧ 0.10 ,≦ 5.0 | ≧ 305 | ≧ 40 | - | - |
1/4H | ≧ 0.10 ,≦ 5.0 | 375~470 | ≧ 28 | ≧ 0.10 ,≦ 5.0 | 90~160 | |
1/2H | ≧ 0.10 ,≦ 5.0 | 470~570 | ≧ 15 | ≧ 0.10 ,≦ 5.0 | 130~190 | |
H | ≧ 0.10 ,≦ 5.0 | 570~665 | ≧ 7 | ≧ 0.10 ,≦ 5.0 | 170~220 | |
EH | ≧ 0.10 ,< 0.20 | 620~710 | - | ≧ 0.05 ,≦ 5.0 | 190~230 | |
≧ 0.20 ,≦ 5.0 | ≧ 4 | |||||
SH | ≧ 0.10 ,≦ 5.0 | ≧ 660 | - | ≧ 0.05 ,≦ 5.0 | ≧ 200 | |
C5191 | O | ≧ 0.10 ,≦ 5.0 | ≧ 315 | ≧ 42 | - | - |
1/4H | ≧ 0.10 ,≦ 5.0 | 390~510 | ≧ 35 | ≧ 0.10 ,≦ 5.0 | 100~160 | |
1/2H | ≧ 0.10 ,≦ 5.0 | 490~610 | ≧ 20 | ≧ 0.10 ,≦ 5.0 | 150~205 | |
H | ≧ 0.10 ,≦ 5.0 | 590~685 | ≧ 8 | ≧ 0.10 ,≦ 5.0 | 180~230 | |
EH | ≧ 0.10 ,< 0.20 | 635~720 | - | ≧ 0.05 ,≦ 5.0 | 200~240 | |
≧ 0.20 ,≦ 5.0 | ≧ 5 | |||||
SH | ≧ 0.10 ,≦ 5.0 | ≧ 690 | - | ≧ 0.05 ,≦ 5.0 | ≧ 210 | |
C5212 | O | ≧ 0.10 ,≦ 5.0 | ≧ 345 | ≧ 45 | - | - |
1/4H | ≧ 0.10 ,≦ 5.0 | 390~510 | ≧ 40 | ≧ 0.10 ,≦ 5.0 | 100~160 | |
1/2H | ≧ 0.10 ,≦ 5.0 | 490~610 | ≧ 30 | ≧ 0.10 ,≦ 5.0 | 150~205 | |
H | ≧ 0.10 ,≦ 5.0 | 590~705 | ≧ 12 | ≧ 0.10 ,≦ 5.0 | 180~235 | |
EH | ≧ 0.10 ,< 0.20 | ≧ 685 | - | ≧ 0.05 ,≦ 5.0 | ≧ 210 | |
≧ 0.20 ,≦ 5.0 | ≧ 5 |
*1 Minimum test force is 1.961N
Thickness Tolerances
Unit:mm
Thickness | Our Achievements | Tolerance (width) | ||
---|---|---|---|---|
≦ 400 | ||||
≧ 0.05 | ≦ 0.08 | ±0.002 | ±0.005 | |
> 0.08 | ≦ 0.15 | ±0.005 | ±0.008 | |
> 0.15 | ≦ 0.25 | ±0.007 | ±0.013 | |
> 0.25 | ≦ 0.4 | ±0.010 | ±0.018 | |
> 0.4 | ≦ 0.55 | ±0.012 | ±0.020 | |
> 0.55 | ≦ 0.7 | ±0.015 | ±0.025 | |
> 0.7 | ≦ 0.9 | ±0.020 | ±0.030 | |
> 0.9 | ≦ 1.2 | ±0.025 | ±0.035 |
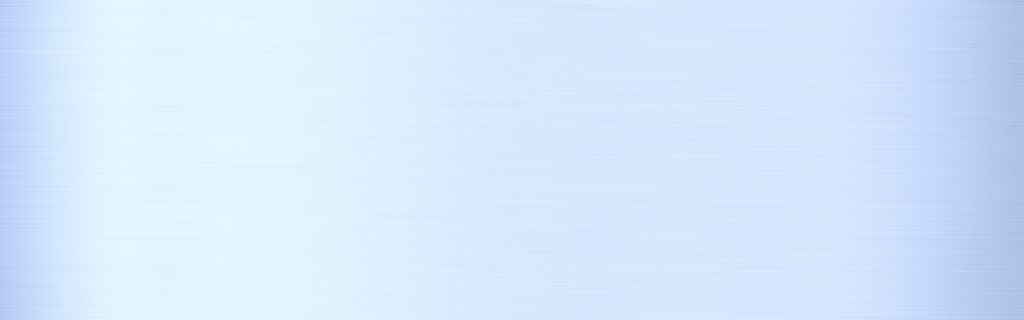
Phosphor Bronze Plates and Strips for Springs
*Please contact us if you have any specific requests regarding chemical composition, mechanical properties, and thicknesses.
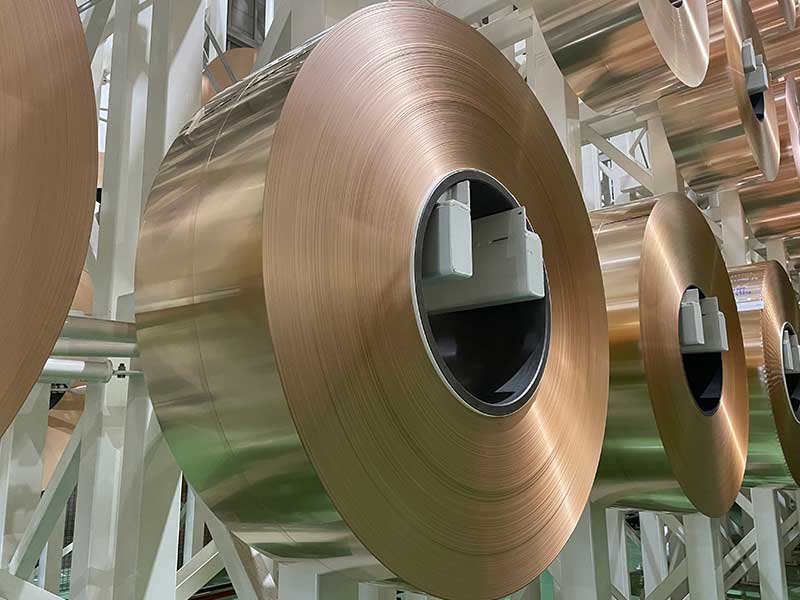
Physical Properties
Alloy Number | (unit) | C5210 | C5240 |
---|---|---|---|
Specific Gravity | - | 8.80 | 8.78 |
Coefficient of Thermal Expansion | 10-6 /K | 18.2 | 18.4 |
Thermal Conductivity | W/m・K | 63 | 50 |
Electrical Conductivity | %IACS | 12 | 10 |
Specific Heat | J/Kg・K | 377 | 375 |
Modulus of Elasticity(Tension) | kN/m㎡ | 110 | 105 |
Chemical Composition
Alloy No. | Chemical Composition(%) | |||||
---|---|---|---|---|---|---|
Sn | P | Fe | Pb | Zn | Cu+Sn+P | |
C5210 | 7.0~9.0 | 0.03~0.35 | ≦ 0.10 | ≦ 0.02 | ≦ 0.20 | ≧ 99.5 |
C5240 | 9.0~11.00 | 0.03~0.35 | ≦ 0.10 | ≦ 0.02 | ≦ 0.20 | ≧ 99.5 |
Mechanical Properties
Alloy No. | Temper | Tension Test | Elastic Limit Test of Spring | Hardness Test | |||||
---|---|---|---|---|---|---|---|---|---|
Thickness Category mm |
Tensile Strength N/m㎡ |
0.2% Yield Strength N/m㎡ |
Elongation % |
Thickness Category mm |
Elastic Limit of Spring (Kb0.1) N/m㎡ |
Thickness Category mm |
Vickers Hardness HV*1 |
||
C5210 | 1/2H | ≧ 0.10 ≦ 1.6 |
470~610 | ≧ 260 | ≧ 27 | ≧ 0.15 ≦ 1.6 |
≧ 245 | ≧ 0.10 ≦ 1.6 |
140~205 |
H | ≧ 0.10 ≦ 1.6 |
590~705 | ≧ 450 | ≧ 20 | ≧ 0.15 ≦ 1.6 |
≧ 390 | ≧ 0.10 ≦ 1.6 |
185~235 | |
EH | ≧ 0.10 ≦ 1.2 |
685~785 | ≧ 580 | ≧ 11 | ≧ 0.15 ≦ 1.6 |
≧ 460 | ≧ 0.10 ≦ 1.2 |
210~260 | |
SH | ≧ 0.10 ≦ 1.2 |
735~835 | ≧ 640 | ≧ 9 | ≧ 0.15 ≦ 1.6 |
≧ 510 | ≧ 0.10 ≦ 1.2 |
230~270 | |
ESH | ≧ 0.10 ≦ 0.40 |
770~885 | ≧ 690 | ≧ 5 | ≧ 0.15 ≦ 1.6 |
≧ 560 | ≧ 0.10 ≦ 0.4 |
245~285 | |
C5240 | H | ≧ 0.10 ≦ 1.6 |
650~750 | ≧ 510 | ≧ 11 | ≧ 0.15 ≦ 1.6 |
≧ 430 | ≧ 0.10 ≦ 1.6 |
200~240 |
EH | ≧ 0.10 ≦ 0.80 |
750~850 | ≧ 630 | ≧ 9 | ≧ 0.15 ≦ 1.6 |
≧ 510 | ≧ 0.10 ≦ 0.8 |
230~270 | |
SH | ≧ 0.10 ≦ 0.40 |
850~950 | ≧ 750 | ≧ 5 | ≧ 0.15 ≦ 1.6 |
≧ 570 | ≧ 0.10 ≦ 0.40 |
250~300 | |
ESH | ≧ 0.10 ≦ 0.40 |
≧ 950 | ≧ 870 | - | ≧ 0.15 ≦ 1.6 |
≧ 630 | ≧ 0.10 ≦ 0.40 |
≧ 270 | |
XSH | ≧ 0.10 ≦ 0.40 |
≧ 1000 | ≧ 930 | - | ≧ 0.15 ≦ 1.6 |
≧ 700 | ≧ 0.10 ≦ 0.40 |
≧ 290 |
*1 Minimum test force is 1.961N
Thickness Tolerances
Unit:mm
Thickness | Our Achievements | Tolerance (width) | |
---|---|---|---|
≦ 400 | |||
≧ 0.05 | ≦ 0.08 | ±0.002 | ±0.005 |
> 0.08 | ≦ 0.15 | ±0.005 | ±0.008 |
> 0.15 | ≦ 0.25 | ±0.007 | ±0.013 |
> 0.25 | ≦ 0.4 | ±0.010 | ±0.018 |
> 0.4 | ≦ 0.55 | ±0.012 | ±0.020 |
> 0.55 | ≦ 0.7 | ±0.015 | ±0.025 |
> 0.7 | ≦ 0.9 | ±0.020 | ±0.030 |
> 0.9 | ≦ 1.2 | ±0.025 | ±0.035 |
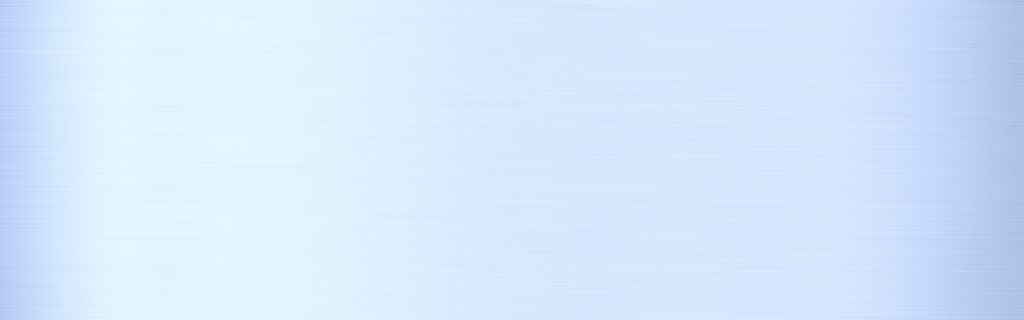
HQ Phosphor Bronze with High Strength and Bending Workability
As electronic devices and parts become smaller and thinner, the need for high strength and precision in the phosphor bronze as the base material also increases.
To meet these needs, we have established a production system for High Quality phosphor bronze with high bending workability (HQ series) in addition to our existing lineup.
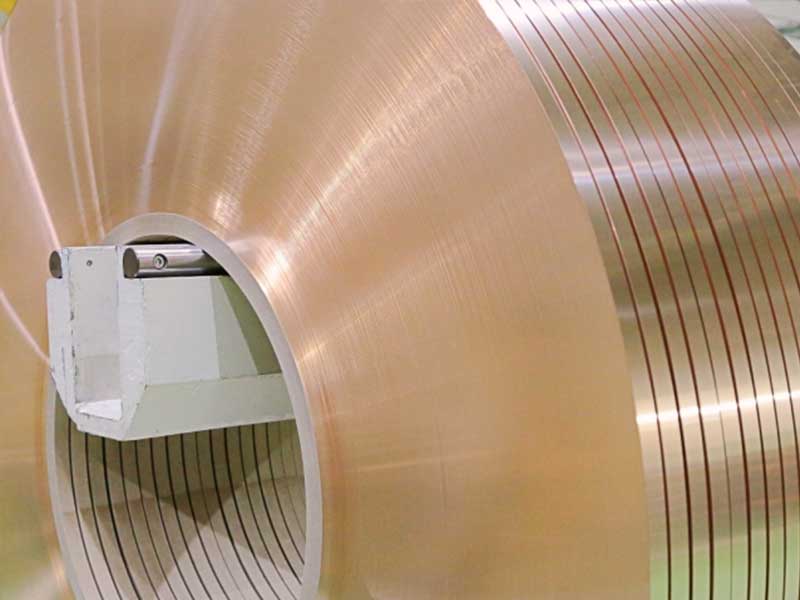
Physical Properties
Alloy Number | (unit) | C5191 | C5210 | C5240 |
---|---|---|---|---|
Specific Gravity | - | 8.82 | 8.80 | 8.78 |
Linear Expansion Coefficient | 10-6 /K | 18.2 | 18.2 | 18.4 |
Thermal Conductivity | W/m・K | 67 | 63 | 50 |
Electrical Conductivity | %IACS | 14 | 12 | 10 |
Specific Heat | J/Kg・K | 375 | 377 | 375 |
Modulus of Elasticity(Tension) | kN/m㎡ | 115 | 110 | 105 |
Chemical Composition
Specifications | Sn | P | Pb | Zn | Fe | Cu+Sn+P |
---|---|---|---|---|---|---|
C5191 | 5.5~7.0 | 0.03~0.20 | 0.01max | 0.01max | 0.01max | 99.8min |
C5210 | 7.0~9.0 | 0.03~0.20 | 0.01max | 0.01max | 0.01max | 99.8min |
C5240 | 9.0~11.0 | 0.04~0.20 | 0.01max | 0.01max | 0.01max | 99.8min |
Standard | ― | 0.03~0.35 | 0.02max | 0.20max | 0.10max | 99.5min |
Product Size
Type | Thickness | Temper | ||||
---|---|---|---|---|---|---|
H | EH | SH | ESH | XSH | ||
C5191HQ | 0.05~0.30mm | ○ | ○ | ○ | ― | ― |
C5210HQ | ○ | ○ | ○ | ○ | ○ | |
C5240HQ | ○ | ○ | ○ | ○ | ○ |
Mechanical Properties
Alloy No. | Temper | Symbol | Tensile Strength N/m㎡ | 0.2% Yield Strength N/m㎡ | Elongation % | Hardness HV | Elastic Limit of Spring N/m㎡ |
---|---|---|---|---|---|---|---|
C5191 | H | Standard | 590~685 | - | 8min | 180~230 | - |
HQ | 630 | 614 | 22.6 | 203 | - | ||
Harada’s average | 620 | 600 | 17.6 | 202 | - | ||
EH | Standard | 635~720 | - | 5min | 200~240 | - | |
HQ | 699 | 697 | 13.7 | 214 | - | ||
Harada’s average | 690 | 662 | 11.0 | 213 | - | ||
SH | Standard | 690min | - | - | 210min | - | |
HQ | 744 | 739 | 12.7 | 222 | - | ||
Harada’s average | 725 | 710 | 8.3 | 216 | - | ||
C5210 | H | Standard | 590~705 | 450min | 20min | 185~235 | 390min |
HQ | 616 | 569 | 35.3 | 197 | 469 | ||
Harada’s average | 615 | 549 | 28.6 | 193 | 462 | ||
EH | Standard | 685~785 | 580min | 11min | 210~260 | 460min | |
HQ | 721 | 694 | 23.2 | 229 | 563 | ||
Harada’s average | 724 | 684 | 17.0 | 228 | 554 | ||
SH | Standard | 735~835 | 640min | 9min | 230~270 | 510min | |
HQ | 778 | 773 | 13.3 | 242 | 632 | ||
Harada’s average | 771 | 756 | 11.4 | 240 | 627 | ||
ESH | Standard | 770~885 | 690min | 5min | 245~285 | 560min | |
HQ | 845 | 834 | 9.3 | 258 | 648 | ||
Harada’s average | - | - | - | - | - | ||
XSH * |
Standard | 835~1000 | - | 1min | - | 630min | |
HQ | 979 | 968 | 2.1 | 285 | 706 | ||
Harada’s average | - | - | - | - | - | ||
C5240 | H | Standard | 650~750 | 510min | 11min | 200~240 | 430min |
HQ | 693 | 657 | 25.6 | 223 | 558 | ||
EH | Standard | 750~850 | 630min | 9min | 230~270 | 510min | |
HQ | 800 | 783 | 15.3 | 245 | 585 | ||
SH | Standard | 850~950 | 750min | 5min | 250~300 | 570min | |
HQ | 890 | 877 | 9.2 | 267 | 661 | ||
ESH | Standard | 950min | 870min | - | 270min | 630min | |
HQ | 1000 | 988 | 2.4 | 285 | 718 | ||
XSH | Standard | 1000min | 930min | - | 290min | 700min | |
HQ | 1058 | 1044 | 2.0 | 305 | 883 |
*Internal standards are shown because the products are not standardized by JIS H3130(2018)
Thickness Tolerances
Unit:mm
Thickness | Our Achievements | Standard |
---|---|---|
≧ 0.05㎜ ,≦ 0.08㎜ | ±0.002㎜ | ±0.005㎜ |
> 0.08㎜ ,≦ 0.15㎜ | ±0.005㎜ | ±0.008㎜ |
> 0.15㎜ ,≦ 0.25㎜ | ±0.007㎜ | ±0.013㎜ |
> 0.25㎜ ,≦ 0.30㎜ | ±0.008㎜ | ±0.018㎜ |
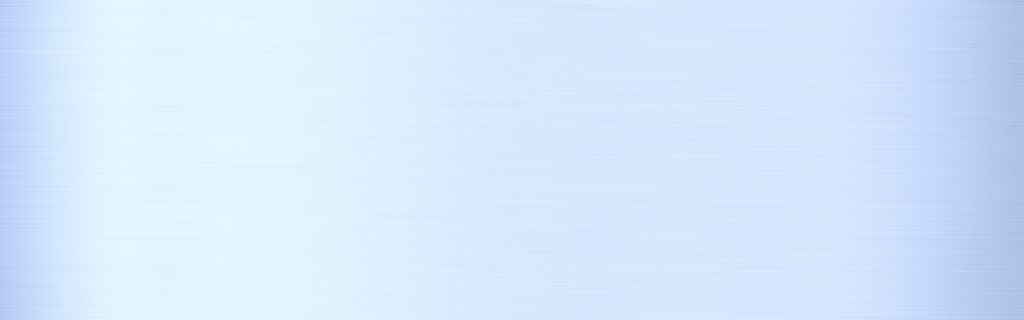
Super-High Strength Phosphor Bronze HC5270
In order to meet the high expectations for higher strength phosphor bronze than ever before, we have carried out research and development of product characteristics and developed the ultra high strength phosphor bronze “HC5270” with a higher tin content of 12%.
We will continue to work to earn the trust of our valued customers by supplying the products required.
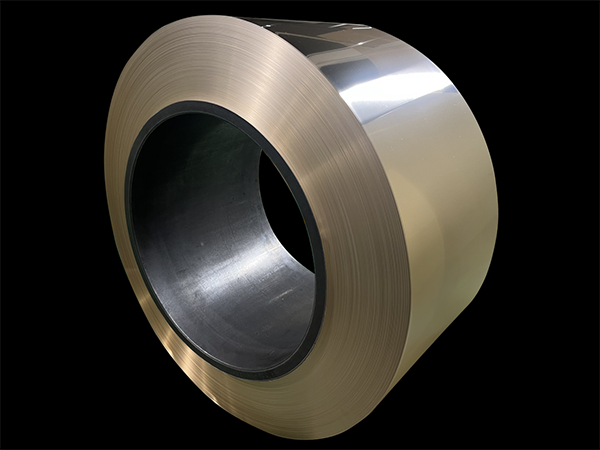
Physical Properties
Alloy Number | (unit) | HC5270 |
---|---|---|
Specific Gravity | - | 8.75 |
Coefficient of Thermal Expansion | 10-6 /K | 18.4 |
Thermal Conductivity | W/m・K | 41 |
Electrical Conductivity | %IACS | 8.5 |
Specific Heat | J/Kg・K | 368 |
Modulus of Elasticity(Tension) | kN/m㎡ | 103 |
Poisson's ratio | ー | 0.33 |
Chemical Composition
Chemical Composition(%) | |||||
---|---|---|---|---|---|
Sn | P | Pb | Zn | Fe | Cu+Sn+P |
11.0~13.0 | 0.03~0.20 | 0.01max | 0.01max | 0.01max | 99.8min |
Product Size
Thickness | Temper | ||||
---|---|---|---|---|---|
H | EH | SH | ESH | XSH | |
0.05~0.20mm | ○ | ○ | - | - | - |
0.05~0.15mm | - | - | ○ | ○ | ○ |
Mechanical Properties
Temper | Symbol | Tensile Strength N/m㎡ | 0.2% Yield Strength N/m㎡ | Elongation % | Hardness HV |
---|---|---|---|---|---|
H | Standard | 750~850 | 620min | 9min | 230~270 |
HC5270 | 812 | 765 | 15.5 | 255 | |
EH | Standard | 850~950 | 740min | 5min | 250~290 |
HC5270 | 895 | 842 | 8.7 | 267 | |
SH | Standard | 950~1050 | 860min | 1min | 270~310 |
HC5270 | 1001 | 949 | 2.3 | 291 | |
ESH | Standard | 1050min | 980min | ー | 285min |
HC5270 | 1109 | 1075 | 1.5 | 307 | |
XSH | Standard | 1140min | 1060min | ー | 310min |
HC5270 | 1213 | 1167 | 1.5 | 354 |
Thickness Tolerances
Thickness | Our Achievements | Standard |
---|---|---|
≧ 0.05 ,≦ 0.08 | ±0.002 | ±0.005 |
> 0.08 ,≦ 0.15 | ±0.005 | ±0.008 |
> 0.15 ,≦ 0.20 | ±0.007 | ±0.013 |